PTAG’s Hydro Experience
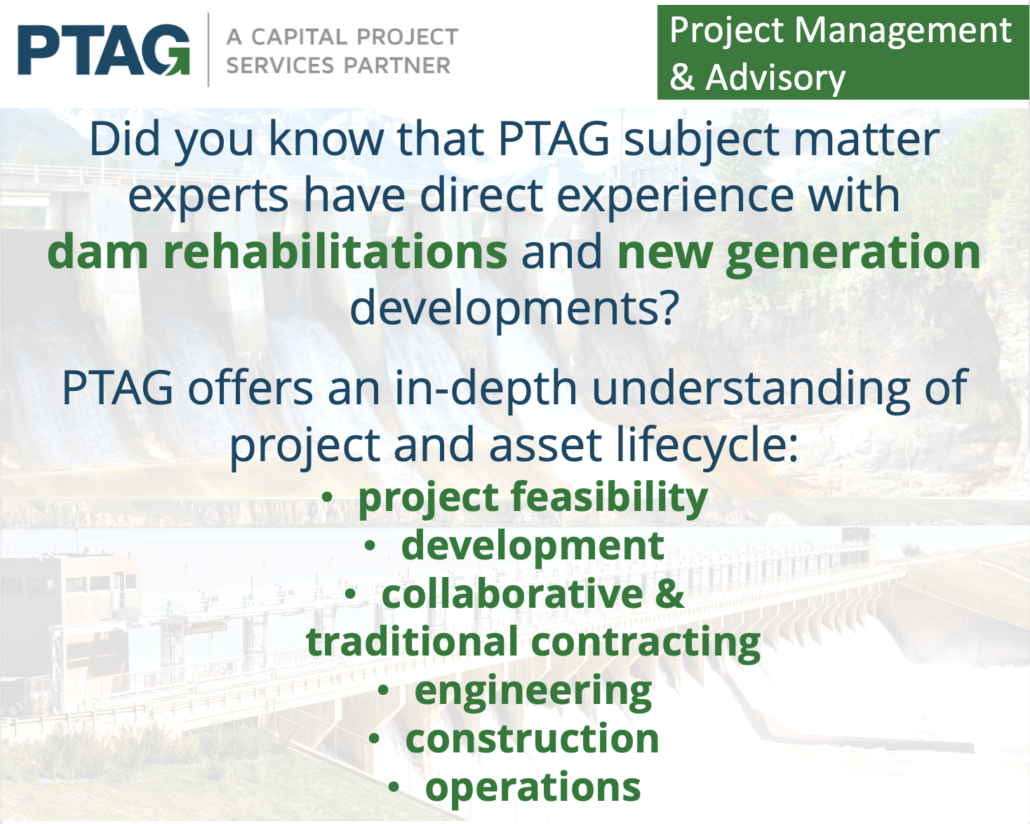
Did you know PTAG has worked on hydroelectric and industrial projects ranging in value from $1M to over $12B and covers:
Hydroelectric development, Rehabilitation, Transmission & Distribution Projects?
PTAG’s Hydroelectric and Industrial Project subject matter experts have direct experience with dam rehabilitations and new generation developments.
PTAG offers an in-depth understanding of project and asset lifecycle, including project feasibility, development, contracting (traditional and collaborative models), engineering, construction, and operations.
Our experienced team’s focus is to help customers deliver project certainty through our experience, best practices, tools, and the team of subject matter experts.
Projects include Coffer Dam installations, Main Dam Concrete, Penstock and underground duct banks projects, Sluiceway and Headgate installations, Bridge construction, Turbine and Generator overhauls and new installations, Transformer, Switchgear, Breaker, Excitation, Protection and Controls installs, 230 & 500 Kv Line, Telecommunication, Control Room and SCADA installations. Service, Domestic Water, Powerhouse and Gantry Crane projects.
“I have been working with PTAG for several years now on collaborative contracting methods. I see them as a leader in project management services and in the new Integrated Industrial Project Delivery model. They provide key services for all types of projects and contract models but it’s their professionalism, creativity, innovative mind set and ability to stay current in this field that sets them apart”.
Alison Bradley, Director, Strategy & Supplier Relationship Management | OPG Supply Chain